By Grant Wilhelm, Senior Design Engineer, CPC (Colder Products Co.)
How quick disconnect connectors evolved for low-pressure fluid handling
The term non-spill, when discussing couplings, describes a specific type of connector meant to reduce spillage to near zero whenever it is disconnected. This is often achieved through the design of the valves housed within the connector body. Originally designed as heavy-duty metal couplings for high-pressure, industrial hydraulic applications, non-spill has evolved into a category of plastic and metal connectors suitable for a variety of fluid-handling applications requiring minimal spillage and air inclusion.

Shift to low-pressure
The original non-spill quick disconnects for high-pressure applications were ball and sleeve coupler packages made from machined brass, zinc-plated steel, stainless steel and aluminum. Because of the high pressures common in hydraulic applications — up to 15,000 psi (1,030 bar) — metals were the only logical material to contain such pressures. Plastic materials came into use because they provide the strength required for lower-pressure applications. Plastics reduce the cost and weight of connectors and answer concerns related to chemical compatibility.
From a design perspective, the traditional characteristics of a non-spill quick disconnect include a flush-face valve design, metal construction and the ability to withstand high pressure ratings. The flush face valve design minimizes the amount of spillage each time it is disconnected, thus the reference as a non-spill connector. This reduced spillage is key to maintaining a clean environment, containing harmful fluids, and protecting workers.

The need to evolve
For some time, low-pressure fluid-handling applications have used non-spill quick disconnects originally designed for high-pressure environments. However, as more low-pressure uses for non-spill connectors emerged, it became clear that high-pressure couplings were over-engineered — and certainly costly — for connecting flexible, semi-rigid and reinforced tubing in low-pressure applications.
To precisely meet the non-spill requirements of low-pressure fluid applications, a new category of couplings has evolved: low-pressure, small- footprint thermoplastic and metal quick disconnect designs that maintain non-spill performance characteristics. The following six traits describe the evolution of the non-spill connector tailored for low-pressure environments.
1. Maintenance of flush-faced valves
The design of non-spill valve technology is not new; what is new is the migration of the flush-faced valve to connectors for flexible tubing used in low-pressure applications.
Connecting and disconnecting in low-pressure environments was historically accomplished with a poppet-style valve (see figure 3). This valve style traps liquid in the valve cavity on the external side of the valve seal. Though the valve has shut off the flow, this remaining volume of fluid can “spill” from the connector. In contrast, the flush-face valve (see figure 3), due to its design, allows no more than a coating of liquid on the valve surfaces, thereby nearly eliminating spillage and ensuring repeated dripless connections and disconnections. Inclusion, or the air put into the fluid system during every connection, is also drastically reduced with flush-face valve design. The benefits of near zero spillage and inclusion have become important in many applications, from medical devices and equipment to chemical handling.
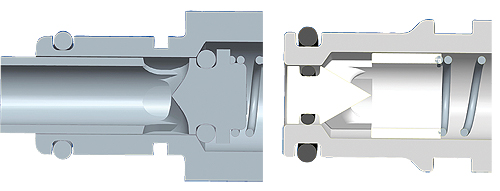
2. Switch from metal to engineered polymers
Metal housings and internal valves were originally chosen for non-spill couplings due to the pressure demands of hydraulic applications. Low-pressure environments do not necessarily require the performance attributes of metal housings and internal valves. Design engineers looking only at metal high-pressure coupling alternatives may be limited in the available selection of weight, package size, flow performance and, in particular, cost. Stainless steel offers the widest chemical compatibility, but is also the most expensive metal choice.
As an alternative, engineered polymers have gained a substantial foothold in applications where metal had been the industry standard. Reduced weight, high strength and rigidity and the ability to achieve complex part geometries are all benefits of engineered polymers. Choosing polymer connectors can provide savings of 50 to 75% compared to metal disconnect products. Some non-spill connectors also incorporate a soft-touch overmold for better ergonomics and color coding (see figure 2). Others feature a glass-filled polypropylene body that offers chemical resistance and increased durability (see figure 4).

3. Low-pressure environments, minimal pressure drop
In low-pressure fluid-handling applications, systems typically operate in the pressure range of vacuum to 120 psi (83 bar). The use of non-spill quick disconnects designed for applications operating in the 10,000 psi range is overkill. A quick disconnect designed specifically for low-pressure fluid-handling applications can deliver all the desirable features of low spillage, low air inclusion and minimal pressure drop. Low-pressure quick disconnects provide higher flow and lower pressure drop compared to their metal counterparts by leveraging the design flexibility gained through the use of plastics and advanced manufacturing techniques, as well as their efficient, high-flow valve design.
4. Compact design
Many low-pressure applications requiring a non-spill connector also demand a compact design, due to both smaller diameter tubing sizes and the interior, or hard-to-access locations, where many non-spill connectors are applied. For instance, non-spill designs used in server racks for liquid cooling or inside in vitro diagnostic equipment need to be as compact as possible to minimize product real estate used and to allow room for technicians to connect and disconnect them.
Today’s increasingly compact connectors are achieved partially through their internal design. Some manufacturers provide non-spill connectors that can connect tubing with an inside diameter as small as 1⁄16 in. or less (see figure 5).
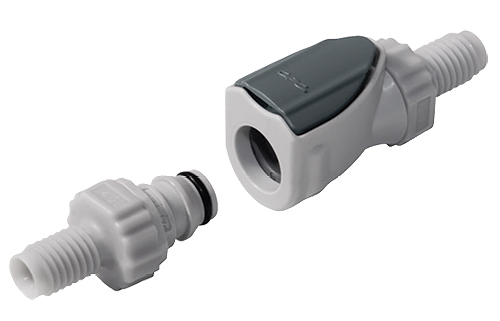
5. Ease of use
An enduring characteristic of high-pressure couplings is the physical difficulty users can have in connecting and disconnecting the couplers. When connecting the couplers, the process can require significant amounts of force. This user inconvenience is addressed in the design of some low-pressure quick disconnects with the introduction of an ergonomic thumb latch that makes the process of disconnecting much easier. Another user benefit provided by some new non-spill connectors is an audible “click” that sounds when a secure connection is made, which confirms for operators that a connection has been made (see figure 5).
6. Chemical compatibility
For certain low-pressure fluid-handling applications, the chemical compatibility of the fluid and the connector, or its parts, needs to be considered. Unlike hydraulic applications—where fluid and metal do not react with each other—low-pressure fluid-handling applications can involve media that reacts with metal. To address this potential concern, connector designers use polypropylene (which offers chemical resistance to many fluids) or other engineered thermoplastics.
Some applications also require a metal-free flow path. One method to achieve this is to isolate the springs from the flow path through the use of an O-ring. This ensures a degree of separation between the fluid and any metal. The O-ring seals separate fluid flow from the valve actuation springs, thereby ensuring high-purity flow paths well suited to applications such as semiconductor manufacturing. In some non-spill connectors, coated springs give a second degree of separation between fluid and metal.
Real-world applications
Many real-world uses of non-spill connectors have evolved from their high-pressure origins. Below are a few examples:
Medical devices and in vitro diagnostic equipment — Many fluid-handling applications for medical devices require minimal air inclusion for accuracy and procedural efficacy. Some devices also require the ability to disconnect tubing without drips or spillage to prevent contact with hazardous fluids and to maintain a safe and clean environment. Analytical equipment used for diagnostics in laboratory or patient care facilities requires the same drip-free disconnect to maintain media integrity, prevent contact with biohazards and maintain a safe working environment.
Ink management — Whether ink is water-based, solvent-based or UV curable, any spillage is a problem. Like water-based inks, solvent-based inks leave a mess, but can also have noxious fumes. Because UV inks only dry under exposure to UV light, small spills wiped up with rags continue to stay wet long after cleanup. Non-spill connectors help keep ink in the system—eliminating the mess at the source—so ink never comes into contact with users or equipment components.
Liquid cooling of electronics — Non-spill connectors are ideal for use in liquid cooling applications. By reducing spillage of water or coolant to near zero, server rack technicians can confidently connect and disconnect them without fear of drips that can damage or destroy equipment. Color coding helps prevent misconnection between hot and cold lines (see figure 1). The latest design features ensure long-term functionality that accommodates prolonged static connections.
The range of non-spill quick disconnects for low-pressure applications continues to grow, from glass-filled polypropylene connectors in increasingly small package sizes to chrome-plated brass non-spills specifically designed for liquid cooling applications. The preceding six evolutionary traits explain why and how today’s non-spill connectors have been designed to meet the unique requirements of low-pressure fluid-handling environments. What started as a high-pressure non-spill coupling has expanded beyond the scope of hydraulics to bring non-spill performance to many industries—and very likely, to products of the future taking shape on CAD program screens today.
Terminology defined
For the purposes of this non-spill technology discussion, the following terminology is frequently used. As with any technical subject matter, it is important to understand and use common reference terminology.
Spillage: The volume of liquid between the valve faces released every time the connector is disconnected. One drop of water = 0.05 ml. A traditional valved 3⁄8 in. coupler has ~ 1 to 3 ml or more spillage per connection cycle; CPC non-spill technology reduces this volume to 0.01 to 0.03 ml spillage per connection cycle with the same 3⁄8 in. flow area, at low pressures.
Inclusion: The volume of air put into a system every time the connector is connected. A traditional valved 3⁄ 8 in. coupler has ~ 2 ml or more inclusion per connection cycle; CPC non-spill technology reduces this volume to ~ 0.4 ml inclusion per connection cycle with the same 3⁄8 in. flow area.
Leakage: Media that leaks out of the connector while connected or disconnected. In a well-designed connector, regardless of its spillage volume specifications, there should be no leakage.
Flow Area: The area through which the fluid or gas media travels. Used to specify coupling size to meet requirements of tubing size, pressure drop, flow rate, and so on.
CPC (Colder Products Co.)
www.cpcworldwide.com
Leave a Reply
You must be logged in to post a comment.